How Often Should You Calibrate Your Test Equipment?
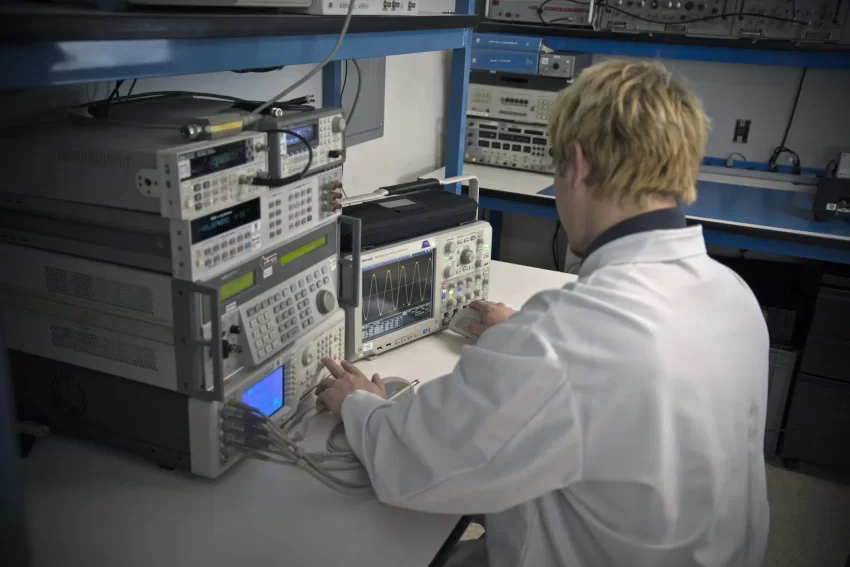
Measurements are the basis of every field. If we want everything to be in order, be it safety, quality, or compliance, we need accurate measurements. Test equipment is an essential part of these measurements. Nevertheless, even the most precise instruments will gradually drift from their original calibration. This leads us to an important question — how often should your test equipment be calibrated? With a proper understanding of it, organisations will be able to be precise and efficient.
Why Does Your Equipment Need To Be Calibrated
A standard reference or an international measurement standard is used for comparison against results derived from measurements made by a device; this process is called “Calibration”. Not only does this help ensure the reliability of the equipment, but it also prolongs its service life. Calibrating your measuring tools routinely is a preventive action to avoid measuring errors that can create a lot of mistakes that cost a lot. Hence, it’s very helpful to know the value that calibration plays in the sustenance of operational excellence. Look for test equipment calibration services to ensure the longevity of your equipment.
Calibration Frequency Control Factors
The frequency of calibration for test equipment is dependent on various factors. This largely depends on the equipment you use, how you use it, and the environmental factors. Calibrating devices operated daily in adverse and harsh conditions will require more frequent calibrating than those in controlled conditions. Additionally, many industry standards and regulations define specific calibration frequencies, considering safety and quality aspects.
Equipment Types and Associated Requirements
Calibration requirements vary between different types of test equipment. Sensitive instruments such as spectrometers require regular calibration owing to their precision nature beds. In contrast, mechanical devices like torque wrenches may require less frequent inspection. A key factor in global calibration planning is the precise requirements of every specific device used in the operations.
Conditions of Use and its Implications
Calibration frequency is hugely impacted by the environment in which equipment operates. Ideal scenarios, such as fast food drive-thrus, facilitate the equipment drift; harsh conditions like high temperatures or humidity can speed it up. Likewise, equipment in high-vibration locations can suffer a higher wear rate. These conditional trends can help guide better decisions on when to calibrate.
Standards and Regulations from the Industry
Various sectors are subjected to certain regulations and standards that determine the calibration frequency. For example, the aerospace, healthcare, and pharmaceutical industries have strict regulations. Not only keeps measurement precision but additionally gives quality. Understanding what departments need to stay current on industry-specific needs. As we mentioned above, keeping up with potential industry penalties over time is important for establishing and maintaining credibility.
Setting up a Calibration Schedule
To establish a calibration schedule, you must evaluate your equipment, its use conditions, and industry guidelines. This schedule is periodically reviewed to ensure it continues to meet operational needs. In addition, keeping a log of previous calibrations may be useful for assessing how the equipment has performed thus far and determining the requirements for future calibrations.
Calibrating Tech With Automated Systems
With advancements in technology, the calibration processes have improved. Automated systems enable more accurate and efficient calibrations, minimising human errors. These advancements empower organisations to optimise their calibration processes, which in turn reduces time and resource consumption whilst maintaining accuracy that touches these processes.
Benefits of Regular Calibration
Regular calibration has many benefits, including better measurement accuracy, safety, and less downtime. Along with keeping a close eye on tolerances, organisations can avoid expensive mistakes and keep uptime on track by not allowing equipment to stray too far from the specified path. Trust from all stakeholders is also built by reliable measurements, which aids the organisation in enhancing its reputation.
Calibration Management Challenges
While calibration management has performed an important role, it can be tricky. Lack of resources, time, and complicated equipment can make it difficult to keep up with regular calibration schedules. These challenges have to be planned for and put in the right order to get tackled. Training and technology can also help you overcome challenges and consistent calibration practices.
Conclusion
Calibration continues to be the key to ensuring the test equipment works properly and provides accurate and reliable readings. Knowing why you should calibrate your instruments for quality and precision and follow the required industry practices will allow an organisation to do so. A well-planned calibration schedule, coupled with the latest technology that allows for optimum equipment usability and reliability, will help you dodge every obstacle and maximise periodic calibration. By doing this, organisations protect operations, build a name brand, and support a culture of excellence.
Leave a Reply