Testing the Limits: The Essential Role of Dynamic Testing Machines in Materials
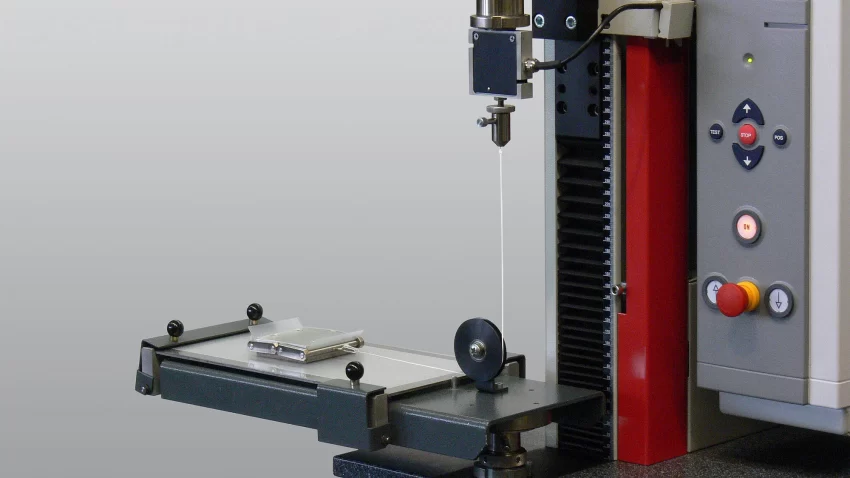
In today’s advancing world, the field of materials science has opened up possibilities for creating safer and more resilient products. Behind every material lies a testing process to ensure its performance under diverse conditions. One crucial tool that plays a role in this process is the testing machine. In this article, we will explore the functions and advantages of testing machines in materials research and development.
1. Understanding Dynamic Testing Machines
A dynamic testing machine is specifically engineered to replicate real-world conditions by subjecting materials to forces like tension, compression, fatigue and torsion. These machines utilise technologies to simulate these loads on samples, providing researchers with vital data on material properties.
2. Evaluating Material Strength
One primary application of testing machines is to evaluate the strength and durability of materials. By subjecting samples to controlled stress or strain scenarios, researchers can determine properties such as ultimate tensile strength (UTS) yield strength, elasticity modulus and other factors necessary for designing dependable products.
3. Assessing Material Response Under Varying Loads
Materials experience types of loads throughout their lifespan.
Dynamic testing machines are designed to replicate loads by utilising adjustable drive systems that apply different forces to samples. This feature enables researchers to assess how materials react under stress or cyclic loading conditions.
4. Examining Fatigue Resistance
Fatigue failures contribute significantly to breakdowns in industries like aerospace and automotive engineering. Dynamic testing machines enable researchers to investigate a material’s fatigue resistance by subjecting it to repeated load cycles at frequencies and amplitudes until failure occurs, ultimately determining its expected fatigue life.
5. Understanding Fracture Mechanics Properties
In applications where catastrophic failures can have consequences, comprehending a material’s fracture mechanics properties is crucial. Dynamic testing machines aid in analysing toughness crack propagation rates. Fracture energy – vital information for ensuring the reliability of materials used in safety-critical industries.
6. Advances in Non-Testing
Traditionally, evaluating a material’s properties involved testing methods that damaged the samples themselves. However, dynamic testing machines now incorporate destructive techniques like acoustic emission monitoring and advanced imaging technologies. These advancements allow researchers to study flaws or defects without compromising the integrity of the samples.
7. Customised Testing for Unique Applications
One major advantage of testing machines is their ability to adapt to sample shapes and sizes. Whether it’s an implant or a large structural component, these machines can be tailored to suit specific research goals. This flexibility guarantees the testing of materials used in any industry under certain conditions.
8. Driving Innovation and Improvement
By harnessing the capabilities of testing machines, researchers can continually push the boundaries of materials science and engineering. The data obtained from these tests enables optimisation in material design. Assists scientists in creating more efficient products across different industries.
9. Reducing Time to Market
In fast-paced industries, reducing time to market is crucial for gaining an advantage. Dynamic testing machines contribute to this objective by providing precise assessments of properties. Researchers can quickly gather data on how a material performs under loads, allowing for iterations in the design and development process.
10. Improving Product Quality
Through testing using testing machines, manufacturers can ensure the quality and reliability of their products. Understanding how materials behave in conditions allows for material selection and optimisation, resulting in improved product performance and customer satisfaction.
11. Ensuring Regulatory Compliance
Numerous industries must adhere to standards to ensure the safety and consistency of their products. Dynamic testing machines play a role in facilitating compliance by providing data required for regulatory approvals and certifications. These machines enable researchers to gather information on material properties, assisting businesses in meeting requirements.
12. Validating Computer Simulation Models
Computer simulation models are crucial during the design process as they allow engineers to predict behaviour before physical prototypes are created. Dynamic testing machines serve as tools for validating these models by comparing simulated results with world experimental data. This validation process enhances the accuracy of simulations, reducing design errors and minimising iterations.
13. Promoting Material Development
With growing concerns about the environment, sustainable material development has become increasingly important in recent years. Dynamic testing machines assist researchers in evaluating the properties of eco materials, optimising their performance while minimising their environmental impact.
14. Encouraging Collaboration in Research
Dynamic testing machines also foster research efforts among institutions, research organisations, manufacturers and other industry stakeholders. Sharing knowledge and expertise through testing initiatives is crucial for advancing our understanding of how materials behave when subjected to loading conditions.
15. Embracing Technological Advancements to Expand Our Horizons
As technology evolves at a fast rate, dynamic testing machines are keeping pace with the demands of exploring territories. By incorporating state-of-the-art technologies such as high-speed cameras, advanced control systems and real-time data acquisition capabilities, these machines allow researchers to delve deeper into the behaviour of materials and push the boundaries of what can be achieved.
Conclusion
Dynamic testing machines are assets in the field of materials science and engineering. They play a role in assessing material strength, studying fatigue resistance, comprehending fracture mechanics, and advancing destructive testing techniques. By accurately evaluating material properties, these machines support rapid product development, enhance quality assurance processes, and ensure compliance with regulations. Furthermore, dynamic testing machines foster collaboration among stakeholders while driving material development and pushing advancements in our quest for safer and more efficient products.
Leave a Reply